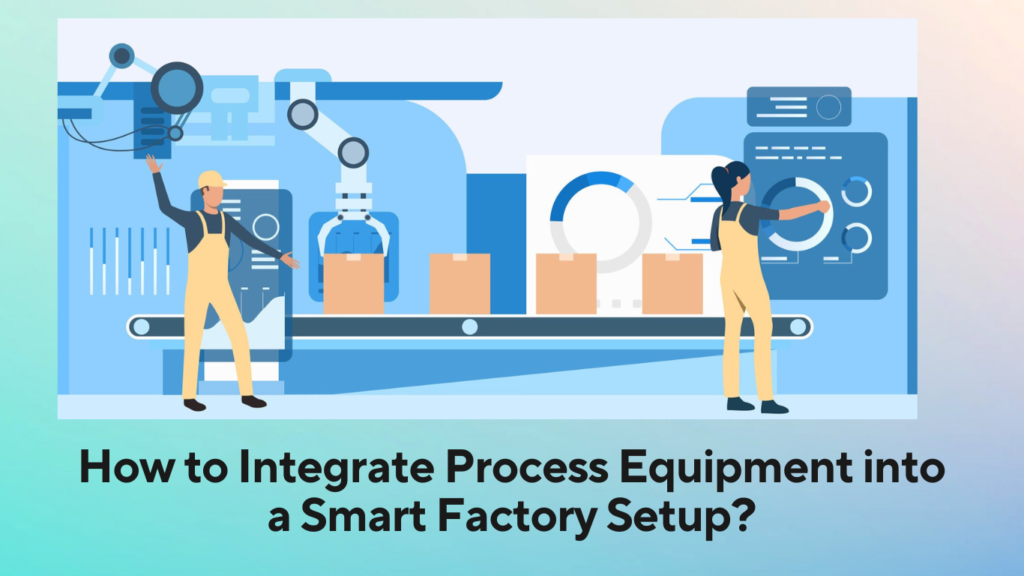
In this day and age, the manufacturing industry in India has been expanding dramatically. Today, many industries are setting up their smart factories to use the latest technology like AI (Artificial Intelligence), automation, or IoT. You can use such technologies to boost your productivity and improve your daily operations.
This needs integration of process equipment into your smart factory setup, your business can achieve greater heights. This transformation requires the right approach, utilising precision engineering services to ensure seamless connectivity and data-driven operations. Read this blog and get to know how you can integrate process equipment into a smart factory setup in India.
Understanding Smart Factory Concepts
Let us decode what is a smart factory concept. It uses advanced technology like IoT, AI, machine learning, and automation to improve the overall production processes. For this, you need to integrate process equipment with the digital systems to allow real-time monitoring and better decision-making. Today, the regular manufacturing units depend mostly on manual intervention and legacy systems. It can often lead to inefficiencies, production delays, and increased costs.
How to Integrate Process Equipment into a Smart Factory
1. Checking Current Process Equipment
You can begin by doing a proper assessment of your existing machinery and its operations. Then identify all the old machines that need to be upgraded and then determine the automation requirements. Next, check for compatibility that can work with the latest digital transformation initiatives.
For example, many factories may lack the latest technology in their machinery which makes the production process very challenging. This is where the precision engineering service manufacturers can help with the upgrades.
2. Selecting the Ideal Technology
Remember to select the right technology that offers balanced technologies like IoT sensors, cloud computing, and AI-driven analytics. With this technology, you are sure to make your existing equipment efficient.
Manufacturers must choose technologies that are scalable and future-proof. For example, IoT sensors should be compatible with multiple platforms to ensure seamless integration. Cloud-based platforms allow for real-time monitoring, while AI-driven analytics provide actionable insights for better decision-making.
3. Implementing Industrial IoT (IIoT)
Industrial IoT enables machines to communicate with each other and with central control systems. By equipping the right equipment with IoT sensors, manufacturers can collect real-time data on performance, energy consumption, and maintenance needs.
IIoT solutions help manufacturers gain visibility into their production process, allowing them to reduce waste, optimise resource utilisation, and improve machine efficiency. Companies like Godrej Enterprises have successfully implemented IIoT solutions to automate their manufacturing units, resulting in increased productivity and cost savings.
4. Ensuring Seamless Connectivity
A smart factory requires seamless connectivity between all machines and systems. Use industrial networks like OPC-UA, MQTT, or Modbus to enable real-time data exchange. This connectivity enhances efficiency and minimises downtime.
A robust network infrastructure ensures that all process equipment operates in sync, reducing delays and inefficiencies. Many Indian industries are now investing in 5G-enabled smart factories to enhance connectivity and improve real-time decision-making.
5. Data Collection and Analysis
Once process equipment is connected, the next step is data collection. Smart sensors and AI-driven analytics tools analyse production patterns, detect inefficiencies, and optimise operations.
Data-driven decision-making allows manufacturers to identify bottlenecks in the production line and take corrective actions before they impact productivity. With the help of precision engineering services, businesses can develop custom analytics dashboards that provide real-time insights into key performance indicators (KPIs).
6. Implementing Predictive Maintenance
With the help of precision engineering services, manufacturers can use AI-based predictive maintenance to prevent unexpected breakdowns. Predictive maintenance tools analyse equipment data to identify potential failures before they occur, reducing downtime and costs.
In traditional factories, equipment failures often lead to production halts, resulting in financial losses. Predictive maintenance helps eliminate unplanned downtime by scheduling maintenance activities based on real-time machine health data. For instance, companies using AI-driven predictive maintenance solutions have reported up to 30% reduction in maintenance costs.
7. Enhancing Automation with AI and Robotics
Smart factories leverage AI and robotics to enhance automation. By integrating robotic arms and automated guided vehicles (AGVs) with process equipment, manufacturers can achieve higher productivity and precision.
AI-powered automation reduces human error, improves quality control, and enhances production efficiency. Robotics also play a key role in automating repetitive tasks, freeing up human resources for more strategic roles.
8. Training Workforce for Smart Operations
A smart factory requires a skilled workforce that understands digital tools and automation systems. Conduct training programs to equip employees with the necessary skills to operate and manage process equipment efficiently.
Many Indian manufacturers struggle with workforce adaptation when implementing new technologies. By investing in skill development programs, businesses can ensure a smoother transition to a smart factory setup.
9. Cybersecurity and Data Protection
With increased connectivity comes the risk of cyber threats. Implement strong cybersecurity measures, such as firewalls, encryption, and multi-factor authentication, to protect sensitive manufacturing data.
Cybersecurity is a crucial part of smart industrial integration. Any weakness in the system might result in data breaches, production halts, and financial losses. Indian firms must establish strong cybersecurity policies to protect their digital assets.
10. Scaling and Future-Proofing the Setup
Your business is a continuous journey and you need to level up your business to a smart factory. Try to update the existing technologies that will help you get a better client base and a higher name in the industry standard. It also ensures a long-term success.
Scaling a smart factory setup involves expanding automation capabilities, integrating AI-driven solutions, and adopting new technologies like blockchain for supply chain transparency. Businesses that continuously innovate and embrace digital transformation will stay ahead in the competitive market.
Conclusion
Adding process equipment to a smart factory setup is important for Indian businesses today if they want to stay current and competitive in the global market for the long term. Try to employ more precision engineering services, since they may help firms improve automation, efficiency, and data-driven decision-making.